AS 9100 IN SINGAPORE
Certification on Quality Management System is the international management system standard for the Aircraft, Space, and Defense (AS&D) industry.
The standard AS 9100 IN SINGAPORE provides suppliers with a comprehensive quality system for providing safe and reliable products to the aerospace industry. AS 9100 IN SINGAPORE also addresses civil & military aviation requirements the quality standards cannot be compromised and is of utmost importance.
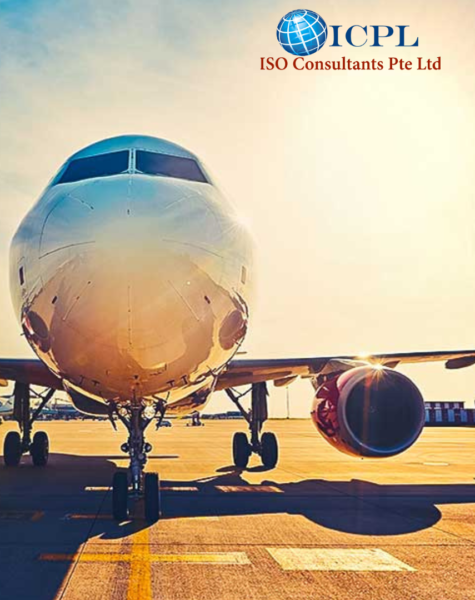
Contact
- ISO Consultants Pte. Ltd. 30 Petain Rd, Singapore 208099.
- +6585993818
- info@isoconsultant.sg
Brochures
View our 2020 ISO 9100
brochure for an easy to read guide on
all of the services offer.
BENFITS OF AS 9100 IN SINGAPORE
STRATEGIC BENEFITS
COMPLIANCE BENEFITS
INTERNAL BENEFITS
- Ability to supply to the aerospace industry
- Positive impact on your bottom line and market reputation
- Recognised certification by an independent certification body
- Establishes a comprehensive system for providing safe and reliable products and services and offers trust throughout the supply chain.
- Reduced costs through improved product reliability, process control and reduction in scrap, rework and rejected products
- Improved employee quality culture and ownership
- Improved risk management with reduction of product or service mistakes and critical failures
CONSULTING STAGES OF AS 9100 IN SINGAPORE
MANAGEMENT OVERVIEW
GAP ASSESSMENT AND PLANNING
DOCUMENTATION
IMPLEMENTATION AND TRAINING
INTERNAL AUDIT AND MANAGEMENT REVIEW
COMPLAINCE
CONTINUAL IMPROVEMENT
- Planning
- Define Context of Organization
- Define Needs and Expectations of Interested Parties
- Define the scope of the Quality Management System
- Define and ensure Management Commitment to the QMS
- Define System Support and Operation Requirements
- Define High Level Processes and System Map
- Define High Level Project Plan
- Define High Level Risks to QMS System Success
- Define initial QMS objectives
- Communication and Training Plan
- Define Internal and External Communication Plans
- Define Training Plans
- Executive and Management Overviews
- Executive and Management Overviews
- Requirements and clarifications of the AS9100D standard
- Applying the Process Approach towards the quality management
- Depiction of the Organization’s Project Plan
- Gap Assessment
- Accurate Gap Assessment of current state vs future state of your QMS
- Utilize the QMS process map as a guide
- Perform Assessments with QMS owners and other stakeholders
- Document Results and Use Results as inputs into the QMS future development
- Planning
- Re-assess planning performed in Phase 1
- From QMS Gap Assessment Findings Revise / Update
- Project Plans
- Communications Plans
- Training Plans
- QMS Policy Development
- Create Level 1 Policy Document
- Involve Leadership in Policy Development
- Include QMS Process Map
- Use as a guide in Policy Development
- Include QMS documents relative to the AS9100D requirements
- Management System and Process Development
- Define Organizational Roles, Responsibilities, and Authorities
- Define Legal Requirements and other Requirements
- Determine QMS Initial Objectives and Develop Plans to achieve them
- Determine Support Requirements relative to your organization
- Establish Training Plans as required
- Establish plan to confirm sufficient awareness and understanding of the QMS throughout all levels of the organization
- Create Quality Management System procedures applying the process approach
- Operational Planning and Control Processes
- Define Performance Evaluation Requirements
- Define Improvement Requirements
- Determine Document Control and Retention Requirements
- Review / Approvals / Document Nomenclature
- Review AS9100 Requirements with appropriate parties
- Implementation
- Develop Implementation Plans
- Quality Management System Training
- All Employee Training
- Management Training
- Functional Area Requirements
- Other
- Internal Auditor Training
- Internal Audit
- Internal Audit procedure and plan
- Based on QMS Processes and Procedures
- Audits by Core and Support Functional Areas
- Internal Audits (Validate QMS Implementation)
- Define Who shall Perform Audits
- Define Audit Schedules
- Communicate Audit Schedules to Process Owners / Auditees
- Perform Audits and Initiate Corrective Actions as Required
- Produce Audit Reports for Management Review
- Management Review
- Plan Management Review Meeting
- Attain all process output and Analyze Data
- Summarize Analyzed Data for Review Input
- Prepare and Summarize Management Review Output Decisions or Actions Required to:
- Improve the Effectiveness of the QMS and its Processes
- Improve worker awareness and knowledge of Quality Management System
- Foster a Continual Improvement Culture
- Close any open actions resulting from Internal Audits or Management Reviews
- Prepare Registrar Assessment Plan with Registrar / Select Guides (Process Owners)
- Schedule the Registrar Assessment and Communicate to Process Owners and Auditees
- Summarize Continual Improvement Activities by Process and Align to
- Business Goals
- QMS Objectives
- QMS Planning Activities
- Measures of Effectiveness
How to Obtain AS 9100 IN SINGAPORE Certification for your Company?